L’azionamento della copertura è gestito da un motore elettrico: azionando un interruttore a seconda di come si preme il tasto, il motore inizierà a funzionare e il suo asse motore ruoterà in senso orario o antiorario a seconda di come fluisce la corrente al suo interno. Fin qui nulla di particolare. la copertura da manuale diventa motorizzata. in questo caso la centralina di comando ha il mero compito di trasformare la tensione di linea (220Vca a 50Hz) in corrente per alimentare il motore a bordo vasca (24Vcc)

Per farla diventare però automatizzata occorre aggiungere qualcosa che permetta a una centralina di “sapere” cosa sta facendo la copertura. In questo caso ci viene incontro l’encoder: un circuito elettronico che ha il compito di dialogare con la centralina per aiutarla a conoscere il comportamento della copertura.
Calettiamo perciò sull’albero motore un disco con dei settori e mettiamo in prossimità un sensore che riesce a leggere quanti settori passano sotto di lui nell’unità di tempo. Questo permette di conoscere quanti giri fa il motore e di conseguenza, tramite software, a sapere quanta strada ha percorso la copertura. Il canale A perciò conosce la velocità ma non sa se la copertura si sta avvolgendo (apertura della vasca) o svolgendo (chiusura della vasca).

Aggiungiamo perciò una seconda pista, sfalsata rispetto alla prima che rappresenta il canale B: in questo caso il sensore deve leggere 2 segnali. Se legge prima il segnale B rispetto al segnale A, la centralina riconosce un verso di rotazione (ad esempio orario) mentre se il sensore legge prima il segnale A rispetto a B la centralina sa che la rotazione è opposta rispetto a prima. La centralina pertanto conosce anche il verso di rotazione.
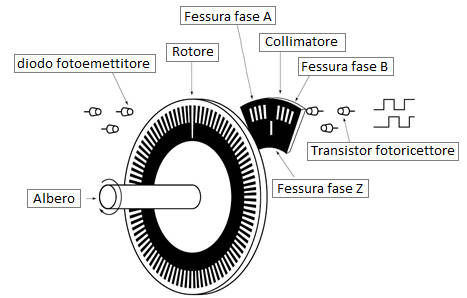

CCW=Antiorario CW=Orario
La precisione è dettata dal numero di settori del disco: maggiore è il numero di settori sul disco, maggiore sarà la precisione di posizionamento dell’albero motore. Per fare un esempio:

Appare chiaro che all’aumentare del numero di settori, è possibile conoscere con maggior precisione la posizione angolare dell’albero.
Ovviamente la precisione della posizione angolare è legata al fattore costo (maggiore precisione comporta un costo proporzionalmente maggiore) ma anche al sistema in cui è installato: nel caso specifico, essendo un motore con elevato rapporto di riduzione, ad ogni giro dell’albero di uscita del riduttore meccanico corrispondono circa 500 giri dell’albero del motore elettrico. Non ha pertanto senso spingersi a risoluzioni estreme dell’encoder.
Un’alternativa è rappresentata dall’encoder di tipo magnetico: utilizza un sistema di rilevazione dei segnali basato sulla variazione del flusso magnetico generato da un magnete (a più coppie polari) calettato sull’albero del motore elettrico di fronte al sensore saldato sulla scheda encoder stessa.
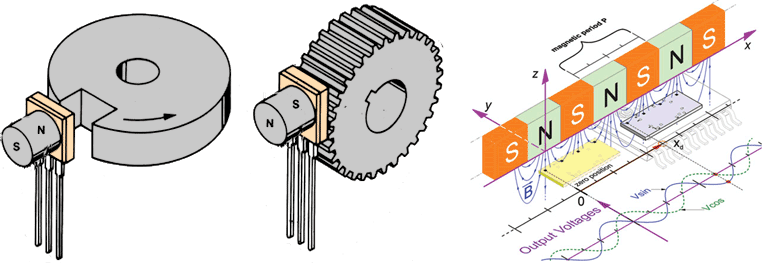
Tra i vantaggi di questa soluzione vi è l’assenza di contatto che si traduce in assenza di usura (non richiede manutenzione ed ha una durabilità potenzialmente infinita). Ulteriori vantaggi sono la resistenza in ambienti gravosi che richiedono un’elevata robustezza, velocità e resistenza termica, garantendo al tempo stesso un’affidabilità ottimale nella generazione dei segnali.
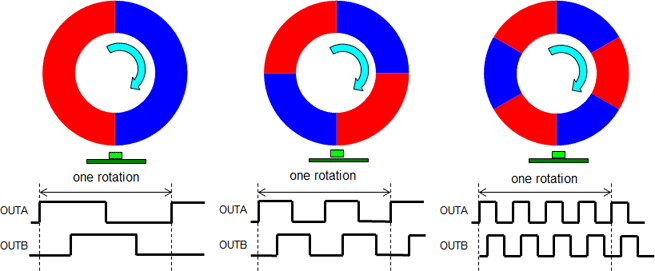
Il segnale sfrutta l’effetto Hall che non è altro che la formazione di una differenza di potenziale (detta tensione di Hall) sulle facce opposte di un conduttore elettrico dovuta a un campo magnetico perpendicolare alla corrente elettrica che scorre in esso. La variazione del campo magnetico determina tale tensione.
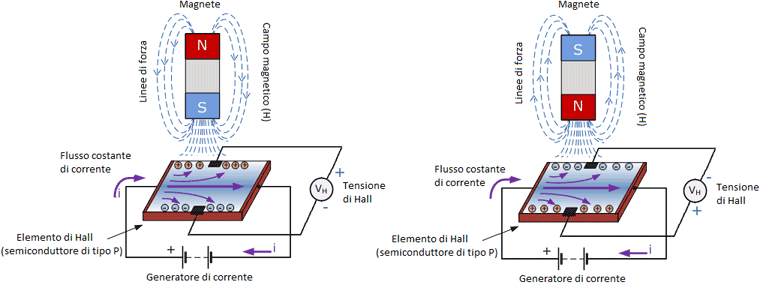
Poiché le tensioni in gioco sono basse, i cavi dell’encoder devono essere schermati per evitare possibili correnti parassite che porterebbero la centralina a non leggere il segnale causando un malfunzionamento del sistema.